The will to wash one’s hands can be easily sidetracked by any one of these situations. Corrective actions in bold.
- Faucet handles: Invisibly contaminated. Go touchless!
- Paper towel dispenser: Invisibly contaminated. Go touchless!
- Soap dispenser lever: Invisibly contaminated. Go touchless!
- Handsink blocked or used for temporary storage. Document with a photo. Discuss with Person-In-Charge.
- Handsink: Visibly soiled. Check cleaning protocol and accountability.
- Slow drain: wastewater splashes. Being used for something other than handwashing? Clean drain.
- Handsink: too far away from critical work station. Add handsink or change food flow.
- Harsh, poor rinsing soap. Change to formulated for frequent-use soap.
- Water too hot or too cold, too slow to adjust. Touchless electronic faucets – safe & time saving.
- Soap dispenser: Empty. Convert to clearly visually cued.
- Refillable hand soap dispenser: Scary appearance. Go closed system!
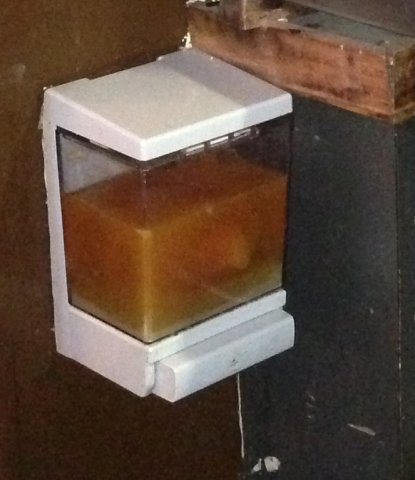
Who is in charge of the handwash station? Design? Purchasing? Quality Assurance? The Person In Charge(PIC)? The Chef? If it’s Operations, who in Operations?
Suggestions:
- Assign the Hand Hygiene Station functionality to a specific person. Include this accountability in their job description. Their role is not to get the staff to wash their hands but to invite use by assuring functionality and cleanliness.
- Use the above as a periodic checklist to identify and resolve recurring issues. Include a summary in the annual report.
- Be sure soap, paper and general handsink cleanliness are on your Opening Checklist.